
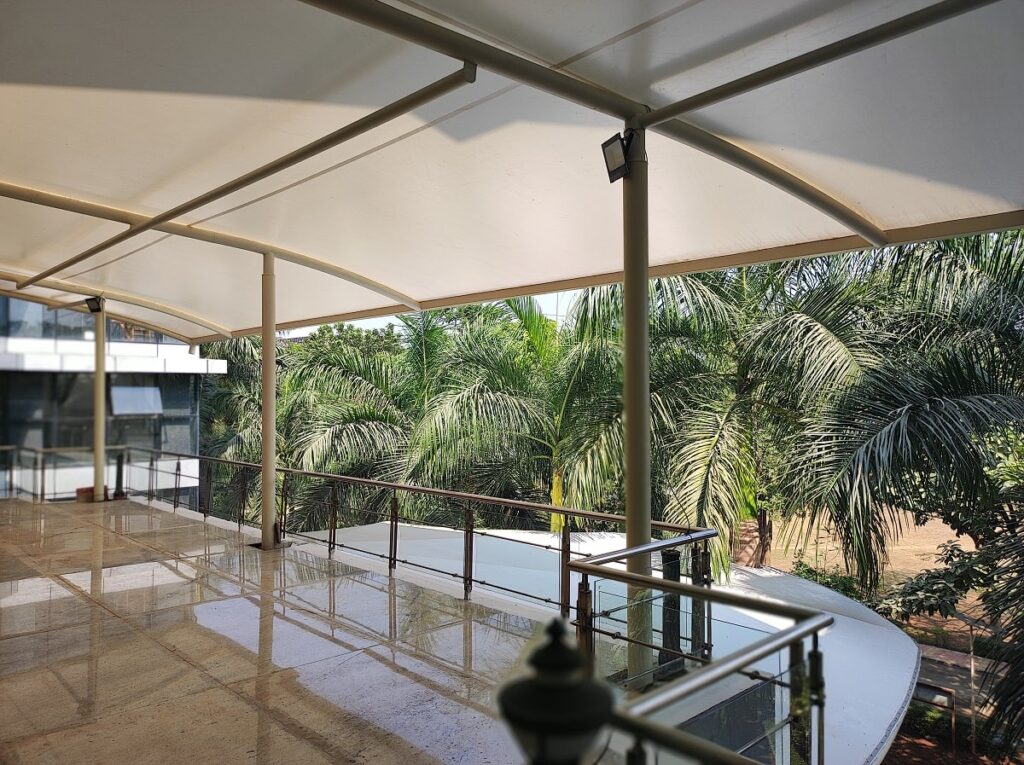
Project Description
Client: ICAR.
Structure design: Dome tensile membrane structure.
Area: 2700 sqft. approx.
Steel: MS dual epoxy coated.
Paint: One coat of Epoxy primer and two coats of Epoxy paint (Asian Paint).
Fabric: 900GSM Sioen(Belgium) PVDF-coated FR Fabric.
Project completion time: 65 days.
Challenges:
- Design Complexity: Tensile membrane structures often have intricate designs that require precise engineering to ensure structural integrity. The challenge lies in creating a design that not only meets aesthetic requirements but also complies with safety and load-bearing standards.
- Tight Project Timeline: Completing the project within 65 days can be demanding, especially when working on a structure as complex as a dome tensile membrane. Delays in any phase of the project, such as design approval, material procurement, or construction, can jeopardize the timeline.
- Quality Assurance for Coatings: The steel components are epoxy coated, and the fabric requires a PVDF coating. Ensuring the quality and uniformity of these coatings is essential for the structure’s durability and appearance.
- Weather and Environmental Factors: Weather conditions can significantly impact construction, especially when working with fabric materials that are susceptible to damage from wind, rain, and UV exposure. Adverse weather can cause delays, affect the quality of coatings, and even pose safety risks to workers.
- Material Sourcing and Availability: Obtaining the specified materials, such as the 900GSM Sioen PVDF-coated fabric, may be challenging depending on local availability and supply chain disruptions.
Addressing these challenges will require effective project management, thorough planning, quality control measures, and the ability to adapt to unforeseen circumstances to successfully complete the tensile membrane structure project for ICAR.
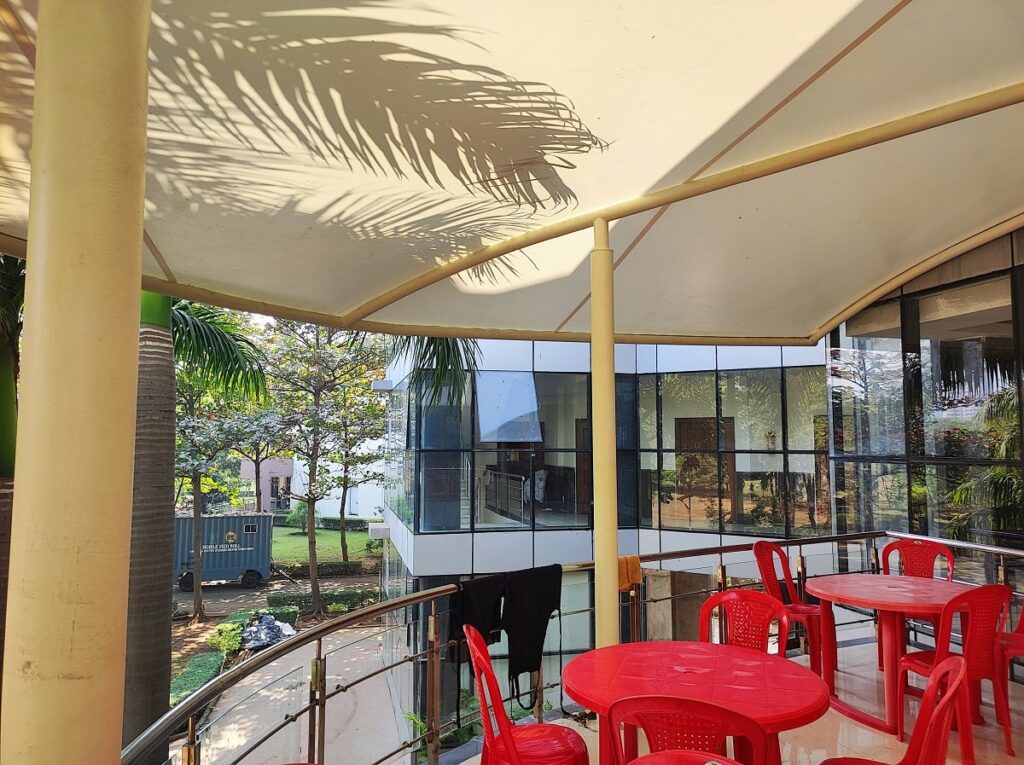


