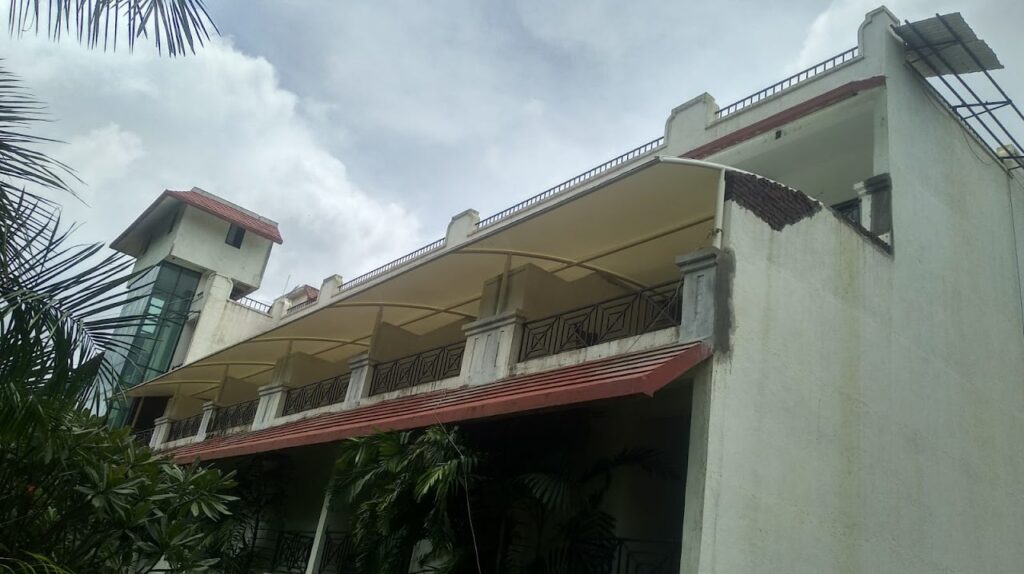


Project Description
Client: Khanvel Resort
Structure design: Arch shape Structure.
Area: 1850sqft.
Steel: MS.
Paint: One coat of Epoxy primer and two coats of Epoxy paint (Asian Paint).
Fabric: Serge Ferrari (French) PVDF-coated FR Fabric.
Project completion time: 20 days.
Challenges:
- Structural Integrity: Ensuring the arch-shaped structure is stable and can withstand environmental forces like wind, rain, and potential seismic activity.
- Material Sourcing and Supply Chain Issues: Acquiring the required amount of MS steel, Serge Ferrari fabric, epoxy primer, and paint within the specified time frame can be a logistical challenge, especially if there are delays in the supply chain.
- Precision Engineering: Achieving the exact curvature and dimensions of the arch requires precise engineering and fabrication to ensure all components fit together perfectly.
- Weather Dependency: Weather conditions can significantly impact construction, particularly if it involves outdoor work. Rain, extreme heat, or other adverse weather conditions may lead to delays.
- Painting Process: Applying epoxy paint requires controlled environmental conditions to ensure a smooth and even finish. Proper ventilation and temperature control may be necessary.
- Fabric Tensioning: Achieving the correct tension in the Serge Ferrari fabric is crucial for both aesthetic and structural reasons. This process may require specialized equipment and expertise.
- Regulatory Compliance: Meeting local building codes, obtaining necessary permits, and ensuring compliance with safety regulations can be a complex process.
- Quality Control: Ensuring that all materials meet the required standards, including testing for the structural integrity of the steel, the quality of the fabric, and the application of the epoxy paint.
- Time Constraints: Completing the project in just 20 days is an ambitious timeline. Coordinating various teams and tasks to stay on schedule is a significant challenge.
- Project Management: Coordinating different aspects of the project, from design and engineering to procurement and construction, requires efficient project management to ensure everything runs smoothly.
- Specialized Labor: Finding skilled workers with experience in constructing arch-shaped structures and working with specific materials like Serge Ferrari fabric may be a challenge.
- Transport and Handling: Managing the transportation and handling of large and potentially delicate components like the arch segments and fabric rolls requires careful planning and execution.
- Quality Assurance Testing: Conduct rigorous testing to ensure that the finished structure meets safety and performance standards, especially considering its unique design.
- Aesthetic Consistency: Ensuring that the final structure matches the aesthetic vision of Khanvel Resort while also meeting all functional requirements.
- Client Communication and Expectations Management: Keeping the client informed about progress, potential delays, and any necessary design adjustments to manage expectations effectively.
Addressing these challenges will require a combination of careful planning, skilled labor, and effective project management to ensure the successful completion of the arch-shaped structure for Khanvel Resort.